|  |
- CamSoft offers various motion boards in various
configurations to meet any Machine Tool Application Requirements. These
are just some of the many possible solutions. Use our Product
Advisor or call our applications engineers to assist you in selecting
the best hardware for your application.
|
CS40000 and CS41030 Series Motion Boards
Ethernet Multi-Axis Motion Controller |
 |
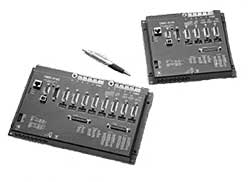
|
DSP Based Ethernet Motion Controller Series CS40000 and CS41030 Motion Control Boxes - Includes: 32
-bit servo/stepper microprocessor motion board, 100 Base-T network interface, optically isolated
digital I/O. Extra auxiliary encoder channels to read handwheels, spindles, turrets or tool changers,
8 analog inputs to read voltages, feedrate pot override or spindle speed override, digital
I/O and DB style terminal cable connections (mounts externally in provided metal box, not
inside computer).
- Comes packaged in a compact, metal enclosure
- Available in 1 through 8 axis models
- Each axis is user-configurable for stepper, PWM or servo motor operation
- Interfaces to a PC with a Ethernet 10/100Base-T cable
- Powerful RISC processor (CS40000 model is 400% faster)
- Runs from 12 VDC source such as the PC power supply
- Encoder frequencies for servos. (CS40000 is 22 MHz), (CS41030 is 12MHz)
- Pulse and Direction output for PWM or Steppers (CS40000 is 6 MHz), (CS41030 is 3MHz)
- Up to 8 main encoder inputs for each servo or stepper axis ordered
- Up to 8 extra encoder inputs. One spare for each servo axis ordered
- 8 Analog inputs for interfacing to analog sensors
- Up to 24 Optically isolated I/O based on axis qty to use for home, forward and reverse over-travel limits. 3 for every axis ordered.
- 1- through 4-axis models provide 8 isolated inputs and 8 isolated outputs
- 5- through 8-axis models provide 16 isolated inputs and 16 isolated outputs
- Up to 16 extra I/O inputs. 1 group of 8 inputs on 1-4 axes models, 2 groups of 8 inputs on 5-8 axes models if spare encoders are not used
- OPTIONAL 32 extra I/O available with CS40000 model
- OPTIONAL Sinusoidal Encoder/Resolver feedback with CS40000 model
Optional Cables
1 meter long cable extends cable length from the DB style terminals. $35 each
7.5 meter long cable that extends cable length from the DB style connectors. $50 each
Screw-on terminal break out boards that plug into DB style terminals. $75 each
- 1 Axis+27 I/O (CS40100 and CS41130)
- 2 Axis+30 I/O (CS40200 and CS41230)
- 3 Axis+33 I/O (CS40300 and CS41330)
- 4 Axis+36 I/O (CS40400 and CS41430)
- 5 Axis+47 I/O (CS40500 and CS41530)
- 6 Axis+50 I/O (CS40600 and CS41630)
- 7 Axis+53 I/O (CS40700 and CS41730)
- 8 Axis+56 I/O (CS40800 and CS41830)
- 1-4 Axes Stand Alone Controller Dimensions - 8.1" X 7.25" X 1.5"
- 5-8 Axes Stand Alone Controller Dimensions - 11.5" X 7.25" X 1.5"
|
|
CS18060 Series Motion Boards
PCI Multi-Axis Motion Controller |
 |
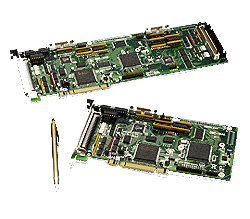 |
If you want the highest performance CNC in the world, this is the one to use.
The new motion board is 10 times faster than our best board we use now and meets or exceeds ALL specs from the world's most expensive controllers at a fraction of the cost.
- Executes motion commands 10 faster than the CS18000
- Theoretical cutting speeds up to 3,000 IPM
- 31 micro second servo update rate per axis
- Reads position feedback 22 million times per second.
- step rate 6,000,000 steps per second
- 1 Axis+19 I/O (CS18160)
- 2 Axis+22 I/O (CS18260)
- 3 Axis+25 I/O (CS18360)
- 4 Axis+28 I/O (CS18460)
- 5 Axis+71 I/O (CS18560)
- 6 Axis+74 I/O (CS18660)
- 7 Axis+77 I/O (CS18760)
- 8 Axis+80 I/O (CS18860)
- 1-4 Axes PCI Board Dimensions - 7.85" X 4.2"
- 5-8 Axes PCI Board Dimensions - 12.28" X 4.2"
|
|
CS18000 Series Motion Boards
PCI Multi-Axis Motion Controller |
 |
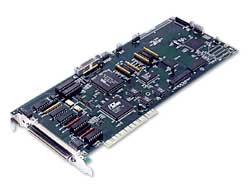 |
Designed to fit in a single PCI slot of a PC, the CS18000 controllers
accommodate 1- through 8-axis formats and allow control of step
or servo motors on any combination of axes. Any mode of motion
can be programmed including linear and circular interpolation.
- Accepts up to 12 MHz encoder frequencies for servos and 3 MHz
for steppers
- Advanced PID compensation with Velocity and Acceleration feed forward,
integration limits. Sample times to 62.5 microseconds per axis
- Modes of motion include jogging, point-to-point positioning,
contouring, linear and circular interpolation
- Home input and forward and reverse limits accepted for every
axis
- 8 Uncommitted inputs and 8 outputs for 1- through 4-axes models,
16 inputs and 16 outputs for 5- through 8-axis models
- 8 uncommitted analog inputs
- Sinusoidal commutation for brush less servo motors
- High-density shielded cables and optical isolation for noise
immunity. CE certified.
- 1 Axis+19 I/O (CS18100)
- 2 Axis+22 I/O (CS18200)
- 3 Axis+25 I/O (CS18300)
- 4 Axis+28 I/O (CS18400)
- 5 Axis+47 I/O (CS18500)
- 6 Axis+50 I/O (CS18600)
- 7 Axis+53 I/O (CS18700)
- 8 Axis+56 I/O (CS18800)
|
|
CS19000 Interconnect Module
Terminal Connection Strip |
 |
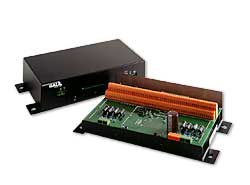 |
The interconnect module provides easy connections between the
CS18000 series controllers and other system elements such as amplifiers,
encoders, and external switches. The CS19000 accepts the 100-pin
main cable and the 25-pin auxiliary encoder cable and provides
screw terminals for quick and easy connection. Use one CS19000
for every four axes (Two required for 5 or more axes). The
CS19000 is contained in a metal enclosure.
- Dimensions - 11.6"" X 7" X 3"
|
Connection Cable
100 pin |
 |
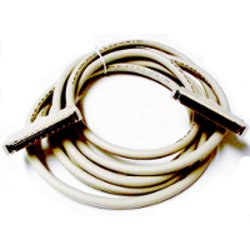 |
|
CS18020 Series |
 |
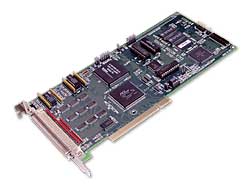 |
Designed for extremely cost-sensitive applications. Performance
specifications are similar to the CS18000 series, but with some
features removed for reduced cost such as uncommitted analog inputs,
a secondary FIFO, optical isolation and auxiliary encoders ( if
you need these features, select the 1800 PCI controller ). Designed
to fit in a single PCI slot of a PC, the controllers accommodate
1- through 4-axis formats and allow control of step or servo motors
on any combination of axes. Any mode of motion can be programmed
including linear and circular interpolation, and contouring.
- Accepts up to 12 MHz encoder frequencies for servos and 3 MHz
for steppers
- Advanced PID compensation with Velocity and Acceleration feed forward,
integration limits. Sample times to 62.5 microseconds per axis
- Modes of motion include jogging, point-to-point positioning,
contouring, linear and circular interpolation
- Home input and forward and reverse limits accepted for every
axis
8 Uncommitted inputs and 8 outputs
- High-density shielded cables and optical isolation for noise
immunity. CE certified.
- 1 Axis+19 I/O (CS18210)
- 2 Axis+22 I/O (CS18220)
- 3 Axis+25 I/O (CS18320)
- 4 Axis+28 I/O (CS18420)
- PCI Board Dimensions - 7.275" X 4.2"
|
|
CS29000 Interconnect Module
Terminal Connection Strip
|
|
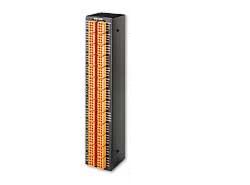 |
The interconnect module provides easy connections between the
Optima series controller and other system elements such as amplifiers,
encoders, and external switches. The module accepts the 100-pin
main cable and provides screw terminals for quick and easy connection.
Use one module for every four axes (Two required for 5 or more
axes). The module has flanges which allow standard screw-type
mounting.
- Dimensions - 13.5" X 4" X 3"
|
Connection Cable
100 Pin Cable |
|
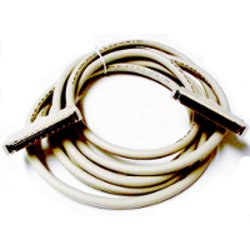 |
|
CS21020 Series |
 |
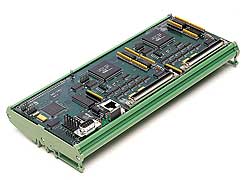
|
These motion controllers for the Ethernet are designed for extremely
cost-sensitive and space-sensitive applications. Performance specifications
are similar to the Optima series, but with some features removed
for reduced cost such as uncommitted analog inputs, optical isolation
and metal enclosure. Available in one through eight axis
versions and can be configured for control of step or servo motors
on any combination of axes. The card-level controller measures
just 4.25" x 7.0" for one through four-axis models and 4.25" x
10.75" for five through eight axes.
This card uses a 100-pin high-density connector for each set of
four axes and requires Connection Cable-100 between the controller
and the CS29000 interconnect module.
- Ethernet connectivity : 10Base-T
- Accepts up to 12 MHz encoder frequencies for servos and 3 MHz
for
steppers
- Advanced PID compensation with Velocity and Acceleration feed forward,
integration limits, notch filter and low-pass filter. Sample
times to 62.5 microseconds per axis
- Home input and forward and reverse limits accepted for every
axis
- 8 TTL uncommitted inputs and 8 outputs for 1- through 4-axis
models; 16 inputs and 16 outputs for 5- through 8-axis models
- 1-4 axes card: 4.25" x 7.0"
- 5-8 axes card: 4.25" x 10.75"
DIN-Rail mount option
- 1 Axis+19 I/O (CS21120)
- 2 Axis+22 I/O (CS21220)
- 3 Axis+25 I/O (CS21320)
- 4 Axis+28 I/O (CS21420)
- 5 Axis+55 I/O (CS21520)
- 6 Axis+58 I/O (CS21620)
- 7 Axis+61 I/O (CS21720)
- 8 Axis+64 I/O (CS21820)
- Optional add 8 Analog Inputs and 24 IO to any CS21020
|
|
CamSoft CS16600 Motion Board $594
|
|
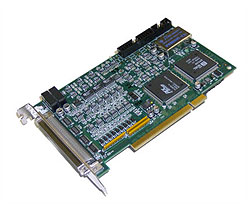 |
CamSofts
motion control card is a low cost solution for servo motor applications. The CS16600 series motion control card installs directly into the PCI bus. This controller series offers many features including 32 bit PCI-Bus, 6 channels 16-bit high resolution analog output, 6 channels 12-bit analog input, 19 channels optically isolated digital input, 7 channels open collector digital output, and 6 differential type 32-bit, 500 kHz encoder or hand wheel inputs. Automatic servo tuning software is included as part of the overall solution using the Graphical OI, CNC Lite or Plus software (call your dealer for availability of CNC Professional). The software also offers a 32,000 position move buffer with unlimited program size.
The CS16600 is capable of controlling up to six axes on a single compact PCI card. These signals can be used for motor control of standard servo motors and amplifiers / drivers with +/- 10 volt analog command signals. The CS16600 achieves superior precision through use of a high resolution 16-bit motor command output DAC and a sophisticated PID filter right on the PC itself. Analog output can also be used for control of spindle drive or as a voltage output source. The card is compact and is only 164mm length by 98.4mm in height.
For synchronization with outside events, the CS16600 provides I/O, including 19 optically isolated 24 volt digital inputs, and 7 optically isolated 5 to 24 volt digital outputs. The CS16600 provides for analog I/O through six analog inputs for use with +/-10 volt differential and single ended signals. Typical Analog input applications would be the use of potentiometers for use in control of speed or feed over ride pots. And any one of the analog axis command outputs can be used as a +/- 10 volt analog output signal for any device requiring a voltage source for control.
Designed as a solution for machine tool control, the CS16600 can be used for applications involving various machine types. Common applications are CNC Mill, Routers, Lathes, Water jets, Lasers, Plasma, Grinders, Punch Press, EDMs, etc. plus Factory Automation.
FEATURES
-
32-bit PCI bus, plug & play card
-
6 High resolution 16-bit +/- 10 Vdc Analog Outputs for Closed Loop Servos, Spindle, Voltage output or Power settings
- 6 Step/Direction for Stepper Motors or Pulse Trains - PENDING -
-
6 thirty two bit High Speed Differential Pulse Counters up to 500 kHz for Encoders or Hand Wheels
- 6 twelve bit Analog Inputs for reading Voltages or Speed and Feed Override pots
- 19 Opto-Isolated Digital Inputs triggered by hardware interrupt
-
7 Opto-Isolated Digital Outputs
|
INCLUDED
- Full Break Out Terminal Strip
- 1.5 Meter Shielded Cable
- Power Cord
- 24 VDC Power Supply
- OPTO22 Relay 3-32vdc input - up to 60V, 5A output
- 32,000 Position Move Buffer with Unlimited Program Size
- Automatic Servo Tuning Software
- Box Dimensions: 5" x 5" x 1.2"
|
|
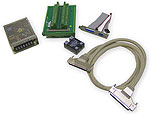 |
|
CamSofts Step Motor Control Card - CS14000
$395 |
|
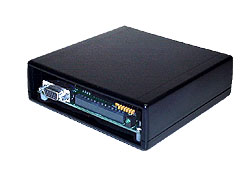 |
CamSofts
Step Motor Control card is a low cost solution for step motor applications. Optionally,
control of brush and brushless servo motors up to 20 amps is available. This
is an external DSP board that generates the step & direction pulses
separately from the computers CPU. Communication is through RS232
serial port. Signal speeds of up to
6,000,000 pulse per minute or 100,000 pps. Using
an example of 4,000 pulses per inch with a 1:1 gear ratio this board
is capable of 1500 IPM cutting feedrate. (You could get less if
your gear ratios or stepper drive requires more pulses per or mm)
-
External
4 axis step and direction board
-
RS232 and power cables
-
6 inputs
-
7
outputs
-
1
over travel input
-
1 E-stop input
-
Speeds up to 6,000,000 ppm
- Box Dimensions: 5" x 5" x 1.2"
|
|
|
|
|
|
|
|
|