CAMSOFT IS THE PERFECT SOFTWARE SOLUTION FOR A NUMBER OF REASONS
You will immediately realize the unmistakable consistency from machine to machine. This is accomplished by using one software package for your entire CNC and general automation machine needs.
Freedom of Choice for the best customizable user interface.
- Standardize your entire operation with one package
- The operator interface is a collection of bitmapped images right down to your logo
- Easily configure each machine to your customer's exact feature specification
- Create an operator interface that simulates your customer's existing controller
- Create your own operator interface or choose from several default operator interfaces
- E-mail a new CBK backup file to enable new features, change the screen or add new G & M codes
- Perform upgrades without the need for a new controller
- Run older G code programs the same way on the new controller without having to edit them
- The G and M codes are in definable tables allowing the system integrator to initially set up his/her own list of G and M codes
- It's possible to simulate as a Fanuc lathe in the morning and an Allen Bradley mill in the afternoon using the same control
- Get spare parts from many sources
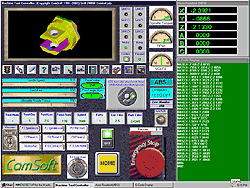
Design your own operator screen. Include your own logo.
The choice is yours
CamSoft offers the best range of choices and prices:
- Select from several ready-to-go control enclosures
- A complete ready-to-go, low-cost hand-held controller
- Motion cards and digital I/O hardware and software available a la carte
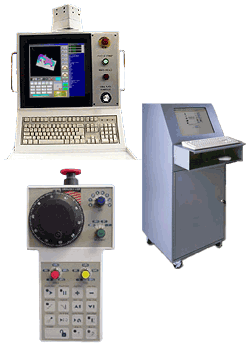
CamSoft offers ready-to-go CNC enclosure pendants and floor models
for every type of machine tool.
Fast , Easy and Reliable
The Finest Dual Processor Hardware
- Hardware is tested and proven with over 200,000 motion cards shipped to date
- 62.5 microsecond servo update times per axis and cutting feedrate velocities of up to 122,000 IPM
- Auxiliary digital I/O cards detect a change of state at rates of 10,000 times per second
- Dual processors allow multiple events and multiple positioning motions to happen simultaneously
- Cut 3D profiles while the tool is changing or a servo motor positions a rotary table
- Dual CPU processor design for extra safety against computer pauses, failures or lock ups
- Dual processors are the best and fastest known method for closing the servo loop with the motors to produce the fastest block-to-block cutting speeds
- Proprietary hardware is not an issue. Spare parts are sold by many companies and most every part of a PC-based controller is off the shelf.
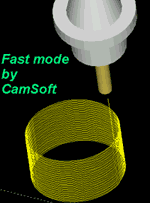
This is a 3D program made up of thousands of G code moves
between .0001 and .020 in length. The Z axis spirals down at a rate of
about .0005 to .0007 tenths. This part was cut at a feedrate of 3,000 IPM.Patent
Pending 3D Tool and 5-Axis Tool Compensation
Patented 3D Tool and 5-Axis Tool Compensation
- The most sophisticated math algorithms & kinematics
- 3D and 5-axis tool compensation G codes at the machine tool with gouge protection
- 3D offset parallel to 3D profile
- 5-axis tool compensation with gouge protection
- 3D part rotation with fixture tilting compensation at the machine itself
*Special post processor required from your CAD/CAM vendor.
Change the tool definitions on the tool parameter screen for a new 3D cutter
just like for G41, G42 in 2D and away you go without G code programming changes in 3D.New G Codes
New G Codes
- The finest user configurable canned cycles
- If you don't see a canned cycle you need, create one yourself
- Place math equations within the G code program by enclosing them within braces.
Included specialized G codes for Mills: G61 and G64 Buffered Look Ahead Spline Mode
G65 Mill Out Rectangular Pocket
G66 Mill Out Circular Pocket
G67 Fly Cut Pattern
G68 Mill Out Rectangular Pocket with Fillets
G120 Mill Outside Square
G121 Mill Outside Circle or Island
G122 Mill Out Counter Bore
G123 Mill Outside Ellipse Pocket
G124 Mill Inside Ellipse Pocket
G125 Mill Outside Slot
G126 Mill Inside Slot
G130 3D Tool Comp with Gouge Protection
G131 3D Offset Parallel to 3D Profile
G135 5-Axis Tool Comp with Gouge Protection
G140 3D Part Rotation and Plane Tilting
G141 Scale Factor for the X Axis Only
G142 Scale Factor for the Y Axis Only
G143 Scale Factor for the Z Axis Only
G160 3D Cylinder
G162 3D Sphere
G163 3D Ramped Plane
G181 Bolt Hole Drill
G182 Bolt Hole Dwell
G183 Bolt Hole Peck
G184 Bolt Hole Tap
G185 Bolt Hole Bore
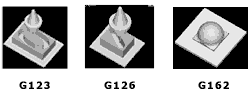
For Lathes:
G110 Lathe Face Groove
G111 Lathe OD Groove
G112 Lathe ID Groove
G113 Lathe OD Thread
G114 Lathe ID Thread
G115 Lathe Rough Face
G116 Lathe Rough Turn
Dynamic Feedrate Control
Automatic adaptive feedrate control combined with the SmartPath option:
- Control cuts at a maximum programmed feedrate
- Controller makes decisions in real time to dynamically adjust feed rate based on cutting conditions
- Controller makes all kinds of variances within a single move to either slow down or speed up in real time
- Feedrates automatically adjust in real time based on spindle torque or feedback from spark gap monitors
- Controller can even change direction based on data acquisition gathered in real time
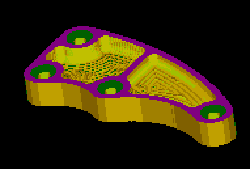
Dynamic look ahead
Advanced Diagnostics
Introducing complete real-time, diagnostic features:
- Axis motor tests, spindle test, digital I/O states, basic servo tuning, analog voltage and position displays, watch windows and remote viewing abilities via a modem directly with CamSoft.
- Hardware items or even logic can be remotely debugged and modified
- Communicate with other machines or other CAD/CAM systems via RS232 or a network
- Optionally press a button on the screen to call for technical help via a modem
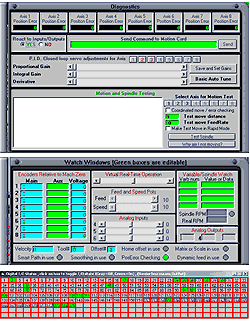
Maintenance/Diagnostic screens allow the user to manually control and view
many factors about the machine itself including servo tuning and all digital I/O states.
Desktop Machine and Logic Simulation
Prove out your machine "virtually":
- Prior to disconnecting the machine wiring, the integrator can virtually run the machine on his/her desktop computer to prove all logic
- Digital I/O events, timed sequential events and logic flows can be tested off line to ensure the machine is properly functioning
- Watch the limit switches trigger and motors position in slow motion to catch and solve problems
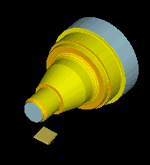
When you are all done, you can run a G code program through the
control on your desktop and watch the tool animation cut the block of material
out of a high-resolution solid model on the screen.
Cut Visual Models, Not Code
The Best new idea and trend since the NC was invented:
- 3D CAD/CAM system and PC-Based Machine Tool Controller share same database in memory
- Part directly cut from graphics on CAD/CAM screen without the need to write post processors or G code files
- Pass graphic picture files of your parts rather than G and M codes
- Screen image drives the machine in lieu of interpretation of codes or G code programs
- Controller shares the same DLLs and ActiveX components with the CAD/CAM system
- Design next part on the screen while machine is cutting current part - initiate Cycle Start when completed
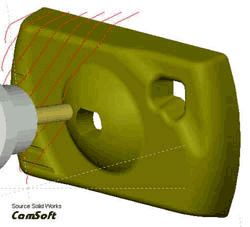
In this mode you can take any picture of a tool path on the screen,
whether it was imported by another CAD/ CAM system or
drawn by you with our CAD/CAM system, and initiate a Cycle Start.
Ball Screw Error & Backlash Compensation
Real-time mechanical error compensation:
- Maps axes in advance for backlash and worn spots to eliminate position errors before they happen
- Upon loading job into memory, system immediately calculates where to move and position corrections ahead of time before you press Cycle Start
- Controller calibrates and maps your axes instead of using a Laser Interferometer and also finds the amount of backlash
Fixture Compensation
Eliminates repositioning of non-flat fixtures:
- Touch off of three points on the fixture to let the controller know the amount the fixture is tilting in a 3D plane
- Skews the program and translates the positions to that plane in 3D
- Rotate a part around any axis in 3D
Crash Barriers
Add extra safety to your application:
- Set up fixture, vise, clamp and chuck crash barriers
- Barrier limits are software-settable for each tool number
- If tool or axes reach or pass the user-defined crash barrier, motion automatically stops
High-speed Rigid Tapping & Lathe Threading
Accurate high-speed precision threads:
- High-speed, precision rigid tapping and lathe threading mode with decelerated stop and reverse
- Rapid to position with forward and reverse coordinated spindle rotation and feedrate control in real time
- Programmable acceleration and deceleration rates for the fastest tapping and threading your machine can handle.
Interruptible Cut-in-progress with Backup
The Best way to backup and restart after an interruption:
- Interruptible "cut-in-progress" feature stops motion and asks the operator to select continue, backup, or abort
- Backup or visually restart using the mouse along the profile past the point of the last cut, replace the tool or restart the spindle, water or flame and press Cycle Start to continue
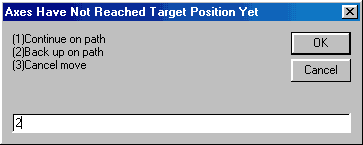
Easily backup and restart after an interruption.
Visually restart mid-program through your part using a mouse or touch screen. This feature reads through the G code program to pick up offsets, tools, fixture positions, speeds, feeds, kerf, tool size and more all the way up to the position you pointed to then prompts you to press Cycle Start when you are ready. This is the easiest and smartest program resume feature we have ever seen. You can even click midway through a cut on a 3D line or arc.
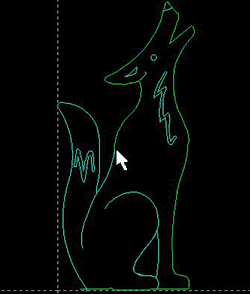
Graphical Mid-program Restart
Set Preferences with Feature Access Limits
The Best way to switch operator interfaces and feature access:
- Swap configurations on the fly with regards to:
working directories
user preferences
visible buttons
feature access
tolerances
metric/inch, and more
- Isolate customer specs, simplify or limit access to features, display information, enable visible buttons and access jobs for each machine operator using the customer name, project name, etc. as a reference or key
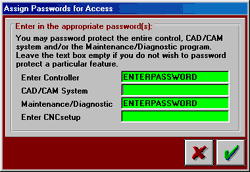
Restrict access to features and programs.
CamSoft controllers are your cost-effective way to give your customers what they want.
- CamSoft controllers understand and read many different G & M code formats
- CamSoft controllers conform to you - no need to edit or rewrite your existing programs
- CamSoft controllers support your existing programs that run perfectly fine on your old machine
- CamSoft controllers can easily restore operator interfaces, I/O logic and G & M code formats within seconds. The operator interface is simply a collection of digital photographed bitmapped images that you can replace.
|